BP Heater Foundation Concrete Repair
Beta Scope
Our scope comprised the following:
- Setting out a programme for the visual inspection, intrusive inspection, assessment, repair design, document submittal and execution.
- Preparing “acceptance criteria” for client approval before carrying out any inspection.
- Preparing the intrusive inspection scope.
- The site inspection and the supervision of intrusive inspection.
- Preparation of structural assessment report and repair design.
- Supervising repairs on site.
One of the main activities in this programme was the assessment and repair design of the regen gas heater pedestal foundation.
Background
Beta Design Consultants acted as structural engineering consultant for Bechtel to carry out the structural inspection, structural assessment and repair design for the civil and structural facilities of BP Rosetta Gas Plant (also known as Giza Fayoum Gas Plant). The plant presented unique challenges due to its location, maintenance history and client requirements. These challenges included:
– The plant is sited on the Mediterranean coast, and was subject to a very corrosive coastal environment.
– The plant function exposed all civil and structural facilities to typically harsh petrochemical conditions (oily and chemical contaminants).
– The plant location near the historic city of Alexandria – a seismic area.
The client’s future plan for the plant required the assessment and life extension of all civil and structural facilities to ensure they have a service life of 25 years.
Challenges
Our pre-inspection meeting with the client set out the criteria for inspection. The condition of any facility was to be assessed on a scale of 1 to 4.
Category | Condition | Description |
1 | Very Good | No concern |
2 | Acceptable | Minor concerns, to be added to asset register maintenance regime |
3 | Poor | Action required, timescale to be agreed |
4 | Very Poor | Urgent action required |
During the visual inspection, it was found that the pedestals of the heater were all found in a very poor condition and as such classified at Category 4 – requiring urgent attention.
Intrusive inspections were arranged to obtain the concrete compressive strength (core crushing), carbonation and chloride ions attached to assess concrete alkalinity and rebar corrosion levels. Tests showed concrete strength to be 30�low design values, carbonation extending to 50mm below surface posing a risk of further chemical attack that could cause more rebar corrosion and undermine pedestals capacity.
Beta Solution
Beta Design Consultants proposed the removal of deteriorated concrete and adding new rebar with a concrete “jacket”. To establish the size of the require jacket, structural analysis was performed using a “composite” section made of an original core with low concrete strength and a jacket of higher concrete strength. The core and the shell would be linked using rebars. Another challenge was maintaining stability during the execution of the works. Removing the heater was not a viable option considering cost and schedule. Supporting the regen gas heater would have also caused delays and costs. An assessment of the weakened pedestal was performed to establish how many pedestals could be repaired at the same time if only temporary wind load and empty heater loads were applicable. The findings allowed the contractor to perform the strengthening for each opposite pair of pedestals concurrently.
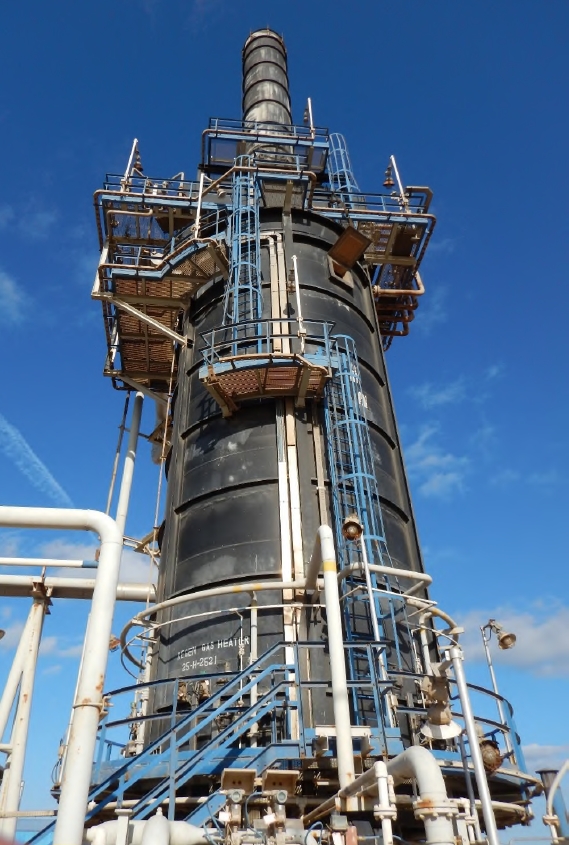